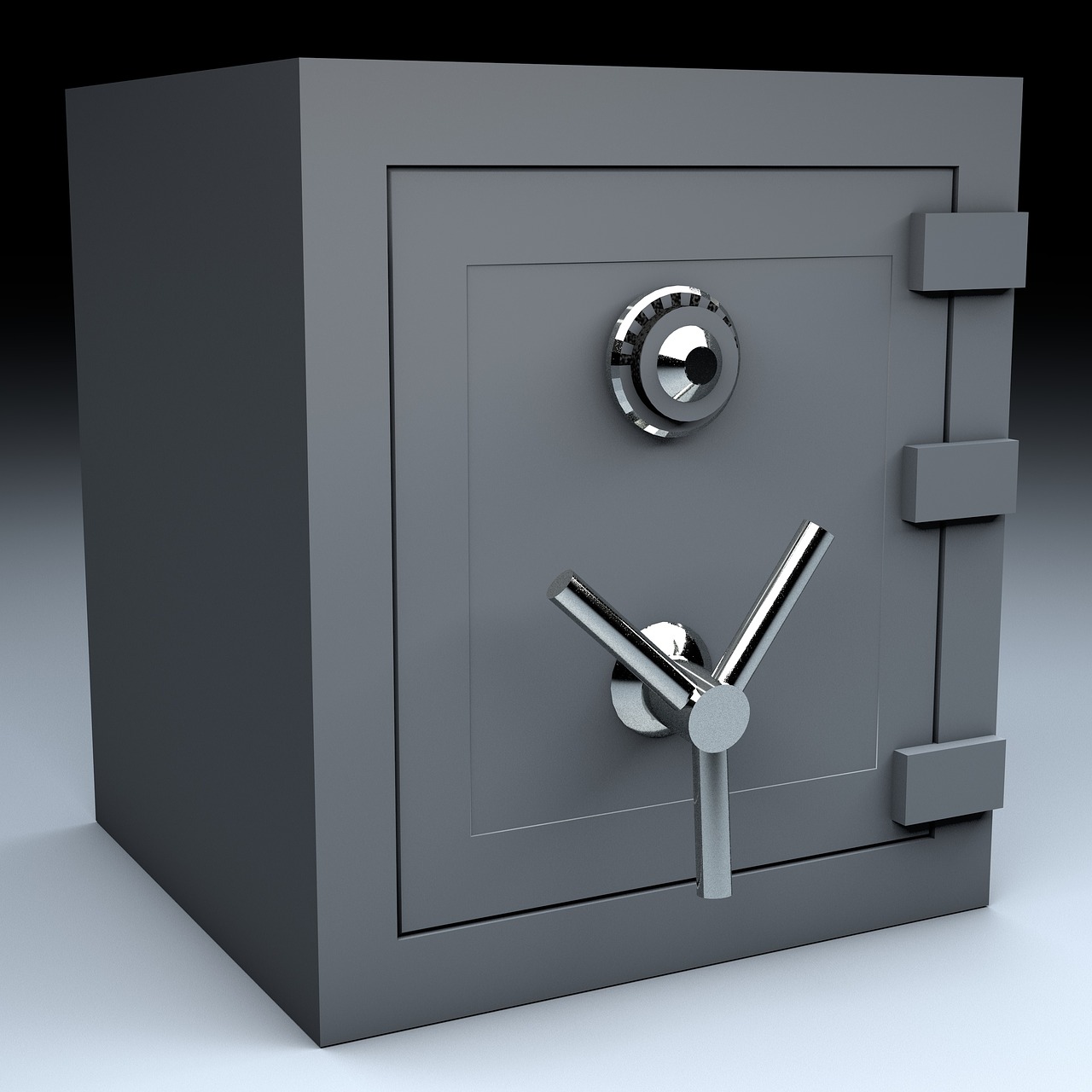
Apart from checking on the standing of the lessee (user of asset), the lessor (owner of asset) has the responsibility of ensuring that the asset under lease is well managed. This is fundamental to the overall achievement of the lessor’s business objective, because the lessee will only be motivated to pay if the asset under lease is in existence and functional. The fact that the lessor has little or no control on the usage of the equipment makes this task difficult.
It is important to pay crucial attention to the following aspects:
- Maintenance of Lessor’s Legal Right: It is not safe to assume that legal ownership of equipment resides with the lessor. Adequate steps should be taken to document lessor’s legal right in the assets. This should start with all documents of purchase. For instance, documents such as bill of lading, official invoices, cash receipt, and other evidence of purchase must be in the name of lessor. The master lease agreement must state categorically that the lessee cannot in any circumstances sell, mortgage, charge, assign, or part with the possession of or otherwise deal with the equipment on lease in any manner inconsistent with lessor’s ownership right. In addition, equipment leased should ordinarily be clearly tagged and labeled by the lessor to further assert its legal ownership.
- Physical Maintenance: This technique of asset management under operating lease remains the most vital of all others. This is so because, it is through adequate and timely maintenance of the equipment that the expected useful life of the equipment can be ensured and probably elongated. It is also true that operating lease agreement will be binding only if the asset is functional. If not, the lessor stands the risk of losing his periodic rentals. Even in finance lease, the lessee will not be motivated to continue rental payment if the asset is not functioning properly and so must ensure that the lessee maintains the equipment appropriately.
Most leasing companies in Nigeria are financial institutions. As a result, the practice whereby a leasing company operates a maintenance workshop for servicing and repairs of equipment on lease is not common. However, some dealer leasing companies have maintenance workshops outlets.
The general practice however, is for the leasing companies to contract the maintenance services to a third party, where the lessees are directed to for regular maintenance and repairs of equipment on lease. For immovable equipment such as factory machinery and in some cases office equipment, the lessor either maintains a standby maintenance team in the factory or contracts the maintenance of the machines to another company that has technical know-how of the equipment involved. In special cases as it is found in the oil industry, maintenance arrangement could involve employing experts who will install and maintain the equipment.
Service report should be maintained in order to have the history of the working condition of the equipment. The basic objective of this approach, is to keep the equipment in a serviceable condition at all times throughout the lease period.
To fully gain foothold on how best to manage your assets, plan to attend ELAN’s Lease Administration Course (From Origination to Termination), 08023176691, 08023179048, info@elannigeria.org, elan_nigeria@yahoo.com